Steel Is Steel, Right?
You are a new fabricator who has just purchased your first press brake. Attached to the side of your brake is an air-bending chart that tells you what tonnage over what size V-die opening you will need to bend various lengths and thicknesses of steel.
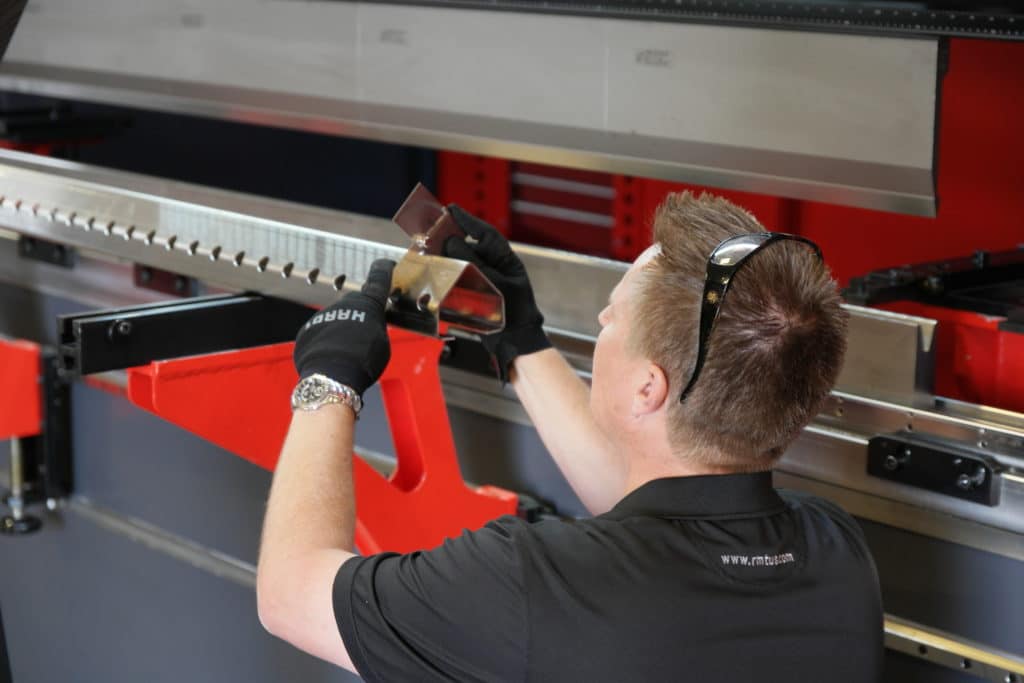
The sales rep showed you a similar chart when you were deciding which brake to buy, and while he was urging you to go a size larger to make sure the machine could handle every job that came your way, you picked the one that was the right size to handle your largest job, determined not to let him talk you into extra bells and whistles like those slick car dealers try.
The only problem is now that you have your machine, it’s not performing the way it should on the larger jobs (hey, maybe he was right about upsizing it after all). Still, you have the right thickness and length of steel to match the chart and it’s still not working. Then you look closer at the chart and see the words “mild steel” displayed prominently. Well that’s just regular steel, right?
You begin to wonder if you are trying to bend the wrong material, so you call up your steel supplier and confirm that it is, in fact, carbon steel that you bought, but that not all carbon steel is the same, and you learn that yours has a higher percentage of carbon than true mild steel. He also tells you about the variances in different types and grades of steel.
You realize that the “one size fits all” mentality you had about your air bending chart wasn’t at all accurate, and you begin to teach yourself to adapt the chart to what you are bending, adding 50% more tonnage for stainless steel, decreasing it for brass and soft aluminum, increasing by quite a bit for bottom bending and coining, making sure your tooling is capable of handling the required tonnage and so forth. (Boy, bending metal is a lot more complicated than you ever realized.)
From Iron to Steel
The Iron Age began four millennia ago when the harder iron began to replace bronze as the go-to metal for making tools and weapons. Over the centuries the usefulness of iron fluctuated, as the advantage of its hardness was offset by its inherent brittleness. As the modern age was dawning in the 17th, 18th and 19th centuries, the understanding of iron’s properties was increasing, alongside its amplified use in structural manufacturing. It was the dawning of the railroad, however, that finally prompted the metallurgic research needed solve the issue of iron’s brittleness by alloying it with carbon to become steel.
The development of the blast furnace by Henry Bessemer in England in the middle of the 19th century revolutionized the production of steel. Inside the furnace iron is heated to a molten state and air is blown through the material to oxidize it and separate out impurities (limestone can be added to react with the impurities to form a slag that floats to the top for removal). Carefully controlling the amount of carbon mixed with the iron makes the alloy stronger without becoming brittle.
Carbon steel, the most common type of steel, contains at least 0.05%—but no more than 2.1%—carbon in its composition. While this is the most common type of steel that is produced, about 10% of steel production accounts for three other main steel types: alloy steel, stainless steel and tool steel.
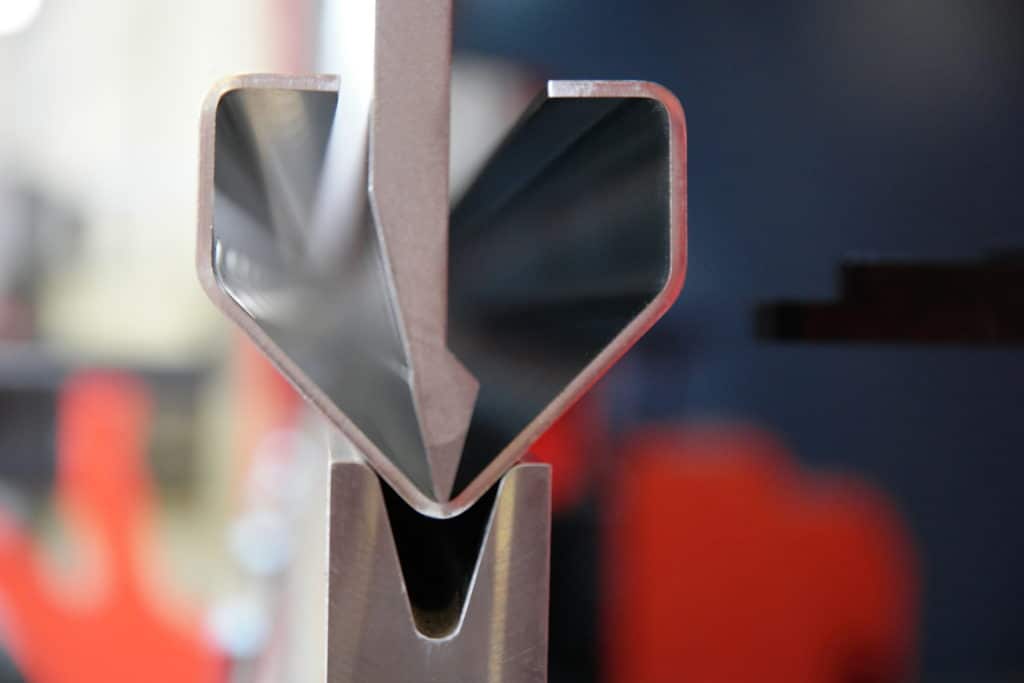
Making the Grade
Most non-metalworkers know there is such a thing as stainless steel that is somehow different from just steel, so learning there are other types beyond those two isn’t much of a stretch. What comes as a surprise to some as they start working in the industry is that each type of steel is broken down into various grades—and not just a few grades, but more than 3,500 different grades!
Having such a seemingly infinite variety of steel may not make much sense to the hobbyist just tinkering in his garage workshop, but these grading standards are relied upon by architects, engineers and scientists alike to guarantee consistency in production and uniformity in applications such as construction.
Different percentages of other metals used in alloys of steel, as well as the very rate at which the steel was cooled, gives each grade unique properties and characteristics.
Spicy? No, I’ll Take My Steel Mild
Carbon steel is classified by three main sub-categories: high carbon steel, medium carbon steel and low carbon steel, which is the type that is commonly known as mild steel. Mild steel contains less than 0.3% carbon, making it very malleable and ideal for cutting, machining and fabricating, as well as being easily welded.
Alloy steel takes its name from being an alloy of not just iron and carbon, but of having other metals or elements thrown in the mix, such as aluminum, chromium, copper, manganese, molybdenum, nickel, silicon, tungsten and vanadium. Low-alloy steel contains between 1% and 8% of other alloying elements and high-alloy steel contains up to 50% of other materials. The different types and percentages of alloying elements changes the properties of the steel, from strength to ductility. Some alloys make the steel more machinable, while others make it more resistant to corrosion.
Stainless steel isn’t just resistant to staining and rusting, but to corrosive reactions in general. Ideal for medical equipment and food processing, stainless steel contains between 10.5% and 20% chromium, most commonly around 11 to 12%. This high chromium content forms an invisible protective layer on the surface of the steel. Stainless steel is broken down into five major types, each defined by its crystalline structure, or the way its atoms are arranged: Austenitic, Duplex, Ferritic, Martensitic and Precipitation Hardening. Each has different characteristics, such as being stronger or more machinable while being less corrosion resistant.
Tool steel, as its name implies, is often used for making tools, especially implements to drill, punch and cut other metals. It is harder, more durable and more heat and abrasion resistant than other steels due to alloying elements such as cobalt, molybdenum, tungsten and vanadium. Tool steel is classified in six general groups based on their properties: Cold work is ideal for cutting or forming materials at low temperatures; High speed is used for tools that have to spin or cut at high velocities; Hot working is for fabricating or cutting materials high temperature; Shock resisting is designed to resist breaking under impact or shock; Water hardening, the most common tool steel, needs to be quenched by water and Special purpose tool steels, which are designed for very specific applications (such as low-alloy special purpose steel which is extremely hard and used for things like shears, spindles, bearings, rollers and precision gauges). Even non-metalworkers will likely have tool steel around their homes in the forms of hammers and knives.

A Steel for Every Occasion
With so many compositions of steel (not to mention specially treated or coated steel, such as galvanized), it is beneficial for every serious metalworker to learn as much as he or she can about the different types and their various uses. Knowing what kinds of steel are appropriate for what projects and being able to identify their characteristics based on their classification and grade will greatly increase the value of any fabricator or machinist in the eyes of their current or potential employers, giving them much greater opportunities in the industry.